数字化转型,快速温变试验箱性能创新探索
数据精准采集与分析,优化控温精度
传统快速温变试验箱在温度控制方面,虽能满足基本温变需求,但在精度把控上存在一定提升空间。数字化转型后,试验箱配备了高灵敏度、高精度的传感器,能够以毫秒级频率实时采集箱内温度数据。这些数据被快速传输至强大的数字化控制系统,借助算法进行深度分析。系统可依据采集数据精准调节加热、制冷装置的功率输出,将温度控制精度提升至 ±0.1℃以内,远高于传统设备。例如在航空航天零部件的超精密测试中,该试验箱能够精准模拟零部件在高空复杂温度环境下的工况,为产品可靠性提供坚实保障,助力航空航天产品突破性能瓶颈。

虚拟仿真预演,缩短测试周期
数字化赋予快速温变试验箱虚拟仿真的强大功能。在实际测试前,技术人员可通过电脑软件构建虚拟测试模型,输入产品的材质、尺寸、预期使用环境等参数,模拟产品在试验箱内的温变过程。软件能提前预测产品在不同温变条件下的物理反应,如热胀冷缩程度、应力分布变化等。通过虚拟仿真预演,技术人员可对测试方案进行优化调整,避免在实际测试中出现因方案不合理导致的时间浪费。以汽车发动机零部件测试为例,以往需多次进行实际测试才能确定温变参数,如今借助虚拟仿真,可将测试周期缩短 40% - 60%,大幅提高研发效率,降低测试成本。
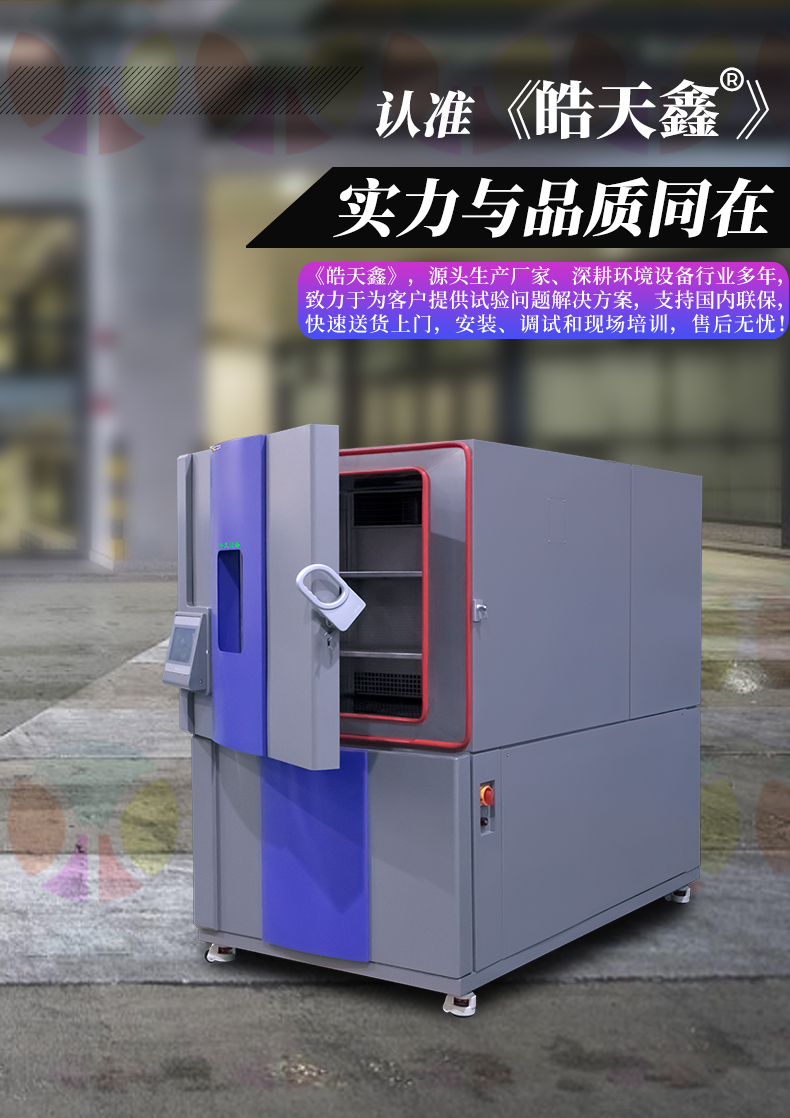
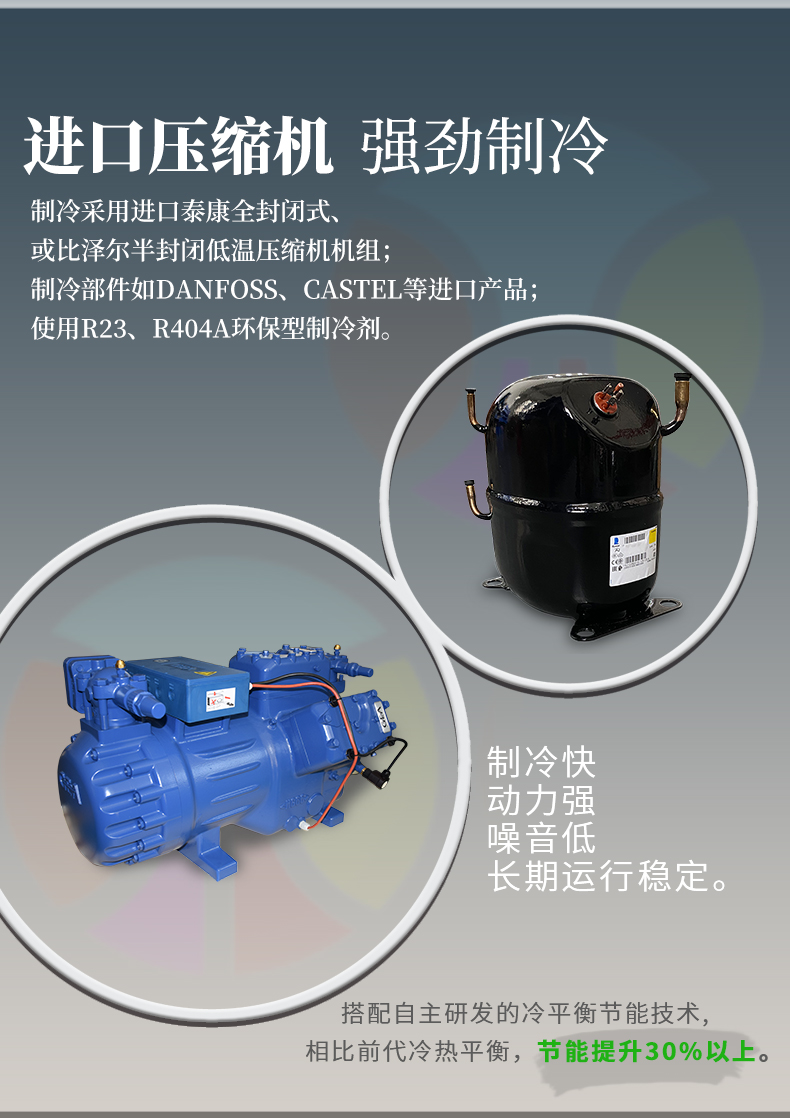
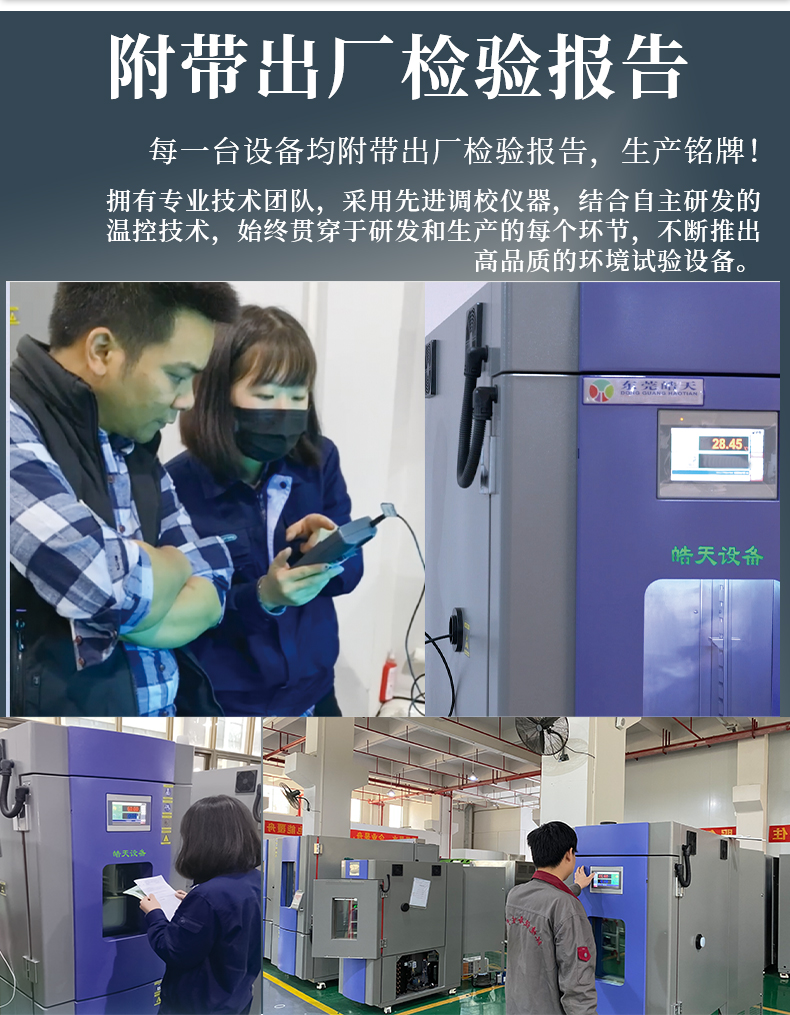
数据互联共享,促进协同创新
数字化转型让快速温变试验箱实现了数据的互联共享。在大型企业或科研机构中,多台试验箱可通过网络连接至统一的数据管理平台。不同部门、不同地区的技术人员能够实时获取试验数据,打破信息孤岛。在电子产品研发过程中,研发团队、测试部门以及质量管控人员可同时在线查看产品在试验箱内的测试数据,共同分析产品性能问题。这种协同创新模式加速了问题解决进程,促进了跨部门合作,推动产品研发迭代升级,使企业在激烈的市场竞争中能够快速响应市场需求,推出更具竞争力的产品。