智能化趋势中,快速温变试验箱性能的变革
智能精准控温,突破传统局限
传统快速温变试验箱在温度控制上,虽能实现基本的温变功能,但在精度与稳定性上存在一定局限。随着智能化发展,如今的试验箱配备智能温控系统。高精度传感器实时采集箱内温度数据,以每秒数十次的频率反馈至控制系统。通过智能算法,系统能精准调控加热与制冷组件,温度控制精度可达 ±0.1℃,远超传统设备。例如在电子芯片测试中,芯片对工作温度极为敏感,智能快速温变试验箱可精准模拟芯片在不同工况下的温度环境,从常温迅速升温至芯片极限工作温度 150℃,且全程温度波动极小,确保芯片性能测试结果准确可靠,助力芯片研发企业攻克技术难题,提升产品性能。
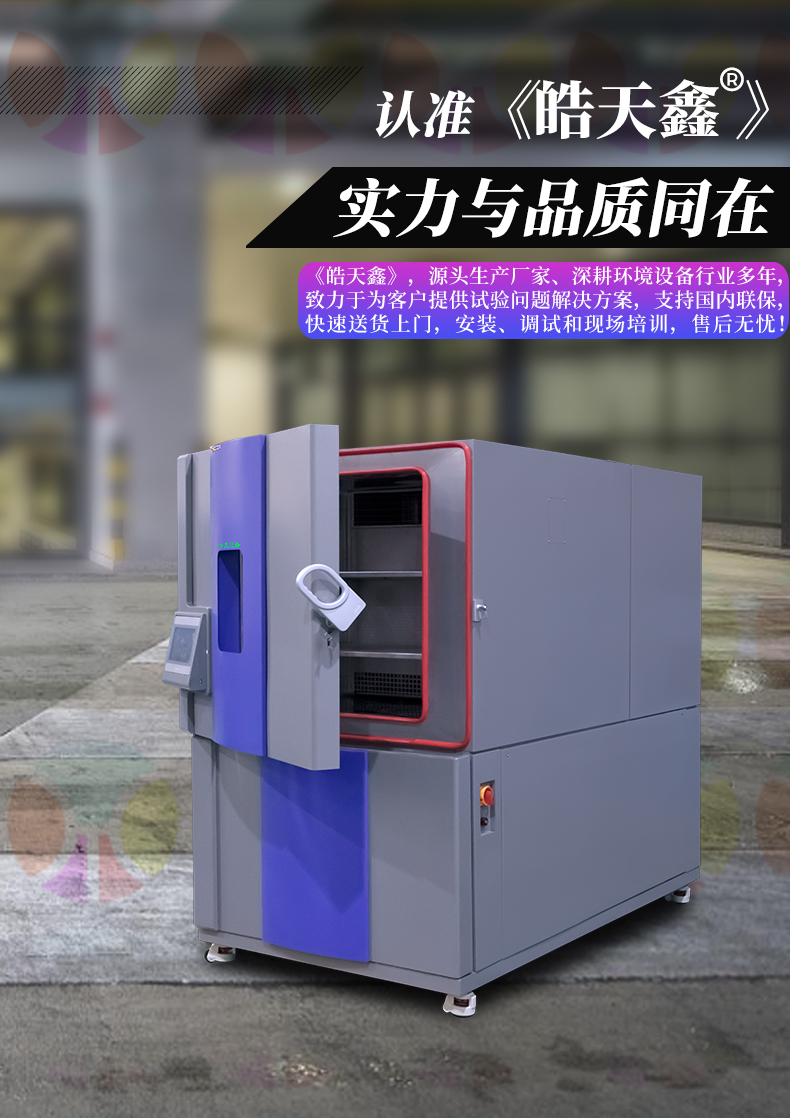
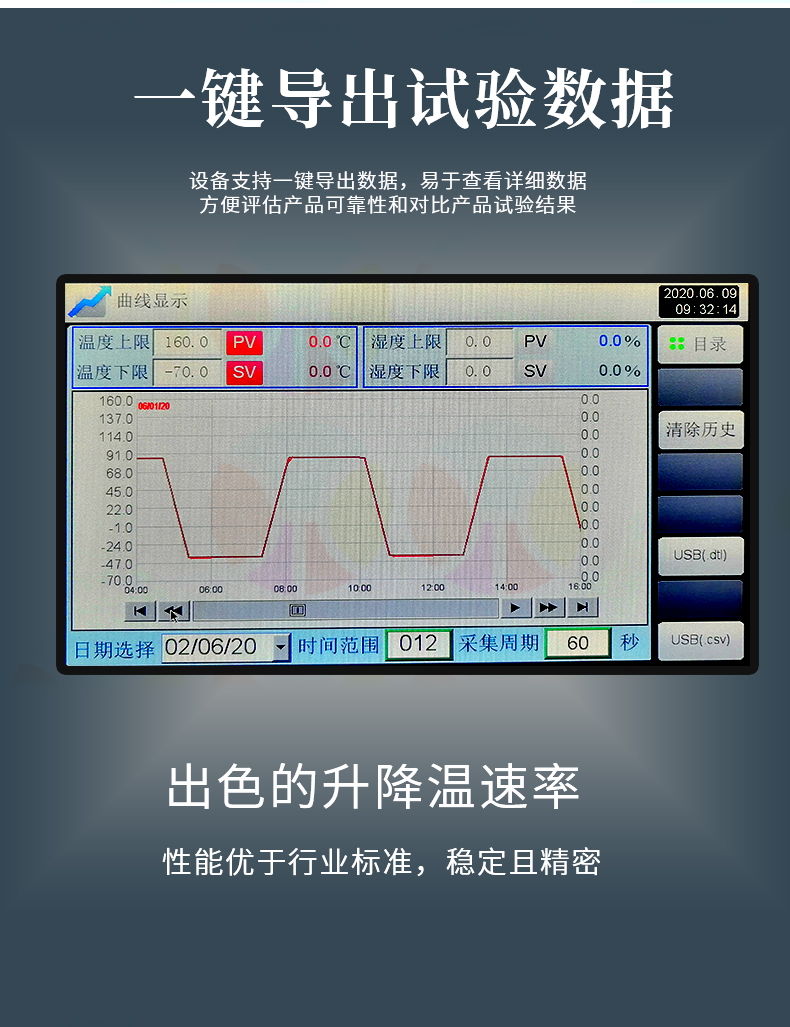
自动化运行,大幅提升效率
智能化让快速温变试验箱实现了高度自动化。以往,操作人员需手动设置复杂的温变程序,频繁监控设备运行状态,不仅耗费人力,还容易出错。现在,试验箱可通过预设程序,自动完成从初始温度到目标温度的快速切换,以及不同温度区间的驻留时间控制等一系列操作。在汽车零部件的可靠性测试中,需对零部件进行上千次的温度冲击循环。智能试验箱能依据预设方案,自动不间断运行,完成一次完整的测试周期时间相比人工操作缩短了 30% - 50%。同时,试验箱还能自动记录测试过程中的各项数据,生成详细报告,极大提高了测试效率,加速产品研发进程。
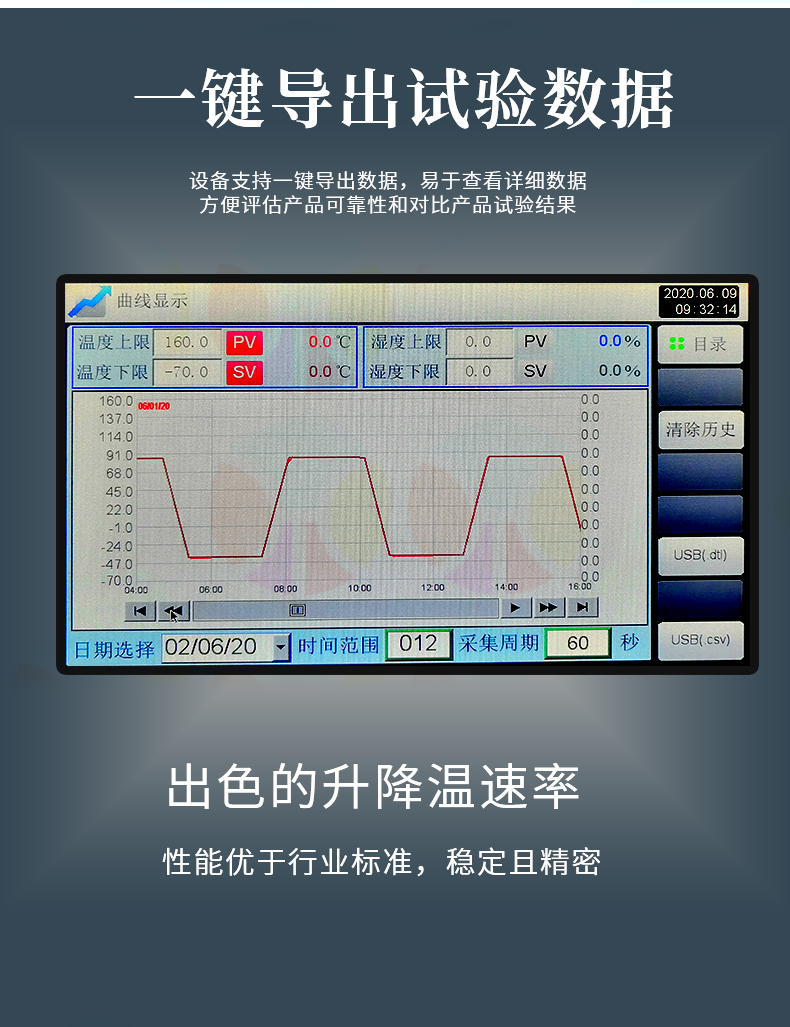
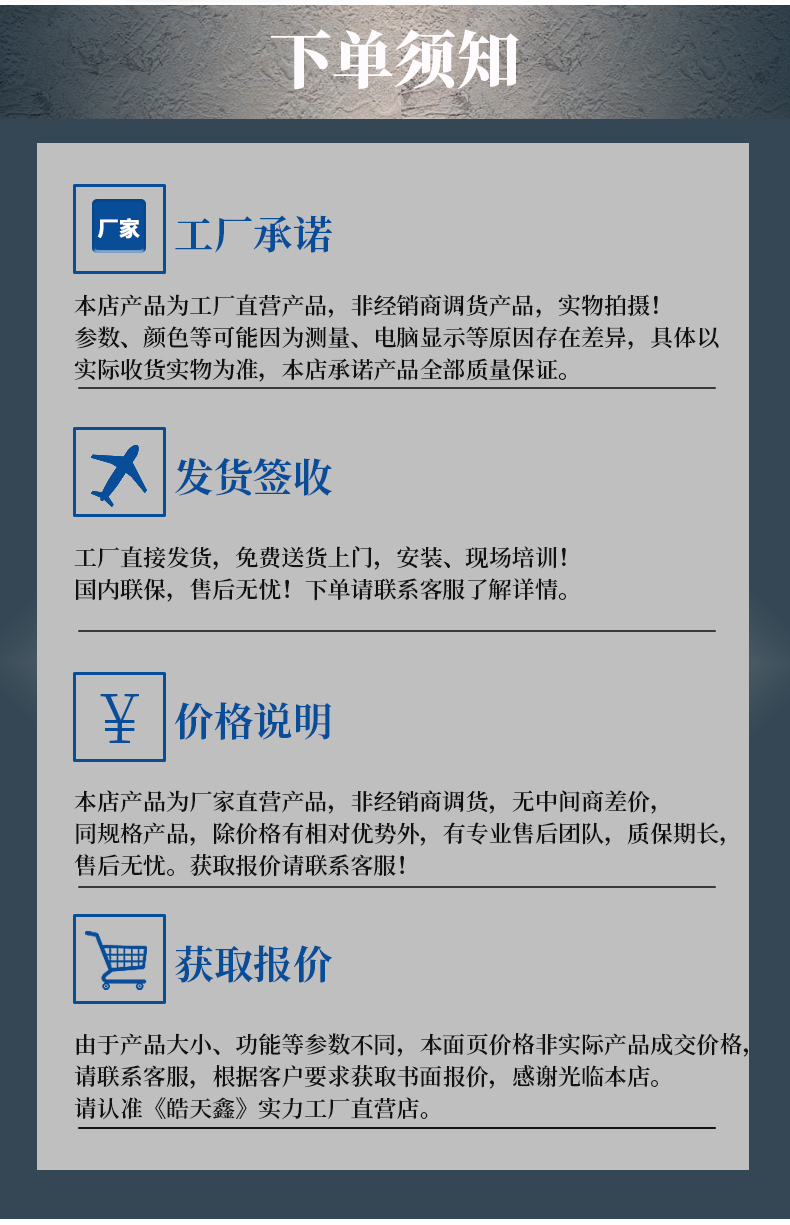
远程监控与诊断,保障设备稳定
借助物联网技术,智能快速温变试验箱支持远程监控与诊断。无论身处何地,操作人员通过手机、电脑等终端设备,便能实时查看试验箱的运行状态,包括当前温度、湿度、运行时间等参数。一旦设备出现异常,系统会立即发送警报信息至相关人员的终端。技术人员可远程连接试验箱,对故障进行诊断与排查,无需亲临现场。这不仅节省了维护时间与成本,还确保了设备的稳定运行。在大型电子制造企业中,多台智能快速温变试验箱分布于不同厂区,通过远程监控系统,管理人员能轻松掌握所有设备状况,及时处理问题,保障生产线的顺畅运行,提高企业整体运营效率。